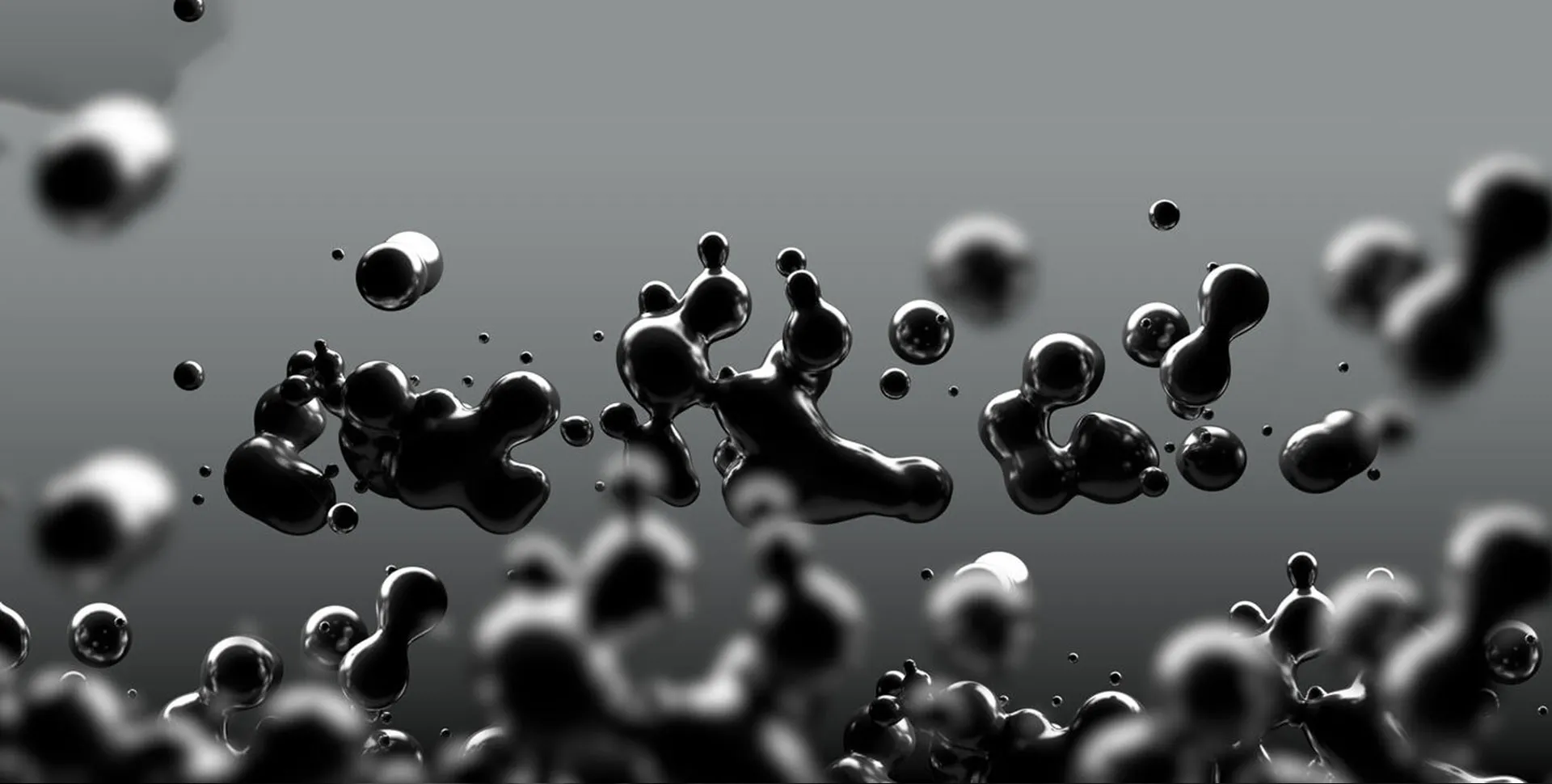
Exploring the Differences Between Basic Carbon Black and Acidic Carbon Black
2024-06-11
I. Introduction
Carbon black is a crucial reinforcing filler extensively used across various industries, including rubber manufacturing, plastics, and coatings. Its primary role is to enhance the mechanical properties of materials, such as tensile strength, wear resistance, and durability. However, not all carbon black is created equal. Two significant types, basic carbon black and acidic carbon black, exhibit distinct properties that influence their performance and applications. Understanding these differences is essential for manufacturers aiming to optimize material characteristics and product performance.
II. Basic Carbon Black: Properties and Characteristics
Definition and Primary Properties
Basic carbon black refers to carbon black that has a higher pH, typically above 7, indicating its basic nature. This type of carbon black is known for its high surface area, porosity, and electrical conductivity. Its basicity arises from the presence of alkaline impurities or surface treatments that impart a basic character.
Production and Applications
Basic carbon black is produced through the incomplete combustion or thermal decomposition of hydrocarbons under controlled conditions. The furnace black process is a common method for its production. Basic carbon black is widely used in rubber products, particularly in tire manufacturing, where it enhances durability and performance. It is also utilized in plastics and coatings for its reinforcing properties.
Structure and Surface Chemistry
The structure of basic carbon black consists of fine particles with a high degree of aggregation. Its surface chemistry is characterized by basic functional groups, such as amine or hydroxide groups, which can interact with polymer matrices, improving adhesion and dispersion.
Advantages and Disadvantages
The primary advantage of basic carbon black lies in its ability to improve the mechanical properties of materials, such as tensile strength and abrasion resistance. However, its basic nature can lead to compatibility issues with certain polymers and additives, potentially resulting in processing challenges and reduced performance in some applications.
III. Acidic Carbon Black: Properties and Characteristics
Definition and Key Properties
Acidic carbon black, on the other hand, has a lower pH, typically below 7, indicating its acidic nature. This type of carbon black is characterized by the presence of acidic functional groups on its surface, such as carboxyl, lactone, or phenolic groups.
Manufacturing Process and Industrial Uses
Acidic carbon black is produced similarly to basic carbon black but may undergo additional treatments to introduce acidic functional groups. This treatment often involves oxidation processes. Acidic carbon black finds its primary applications in industries where specific interactions with polymers are required, such as in certain rubber formulations and specialty coatings.
Structural Features and Surface Characteristics
Structurally, acidic carbon black also consists of fine particles with high surface area and porosity. However, its surface chemistry is dominated by acidic functional groups, which can enhance interactions with certain polymers, improving dispersion and overall material performance.
Benefits and Drawbacks
The benefits of using acidic carbon black include improved compatibility with specific polymers and additives, leading to enhanced processing and performance characteristics. However, the presence of acidic groups can sometimes lead to undesirable reactions with certain materials, limiting its use in specific applications.
IV. Contrasting Basic and Acidic Carbon Black
Direct Comparison of Properties and Characteristics
When comparing basic and acidic carbon black, the primary distinction lies in their surface chemistry. Basic carbon black has alkaline functional groups, while acidic carbon black features acidic functional groups. This difference significantly impacts their interaction with polymers and additives, influencing material properties and performance.
Impact on Performance and Applications
The basicity or acidity of carbon black affects its reinforcing capabilities differently. Basic carbon black tends to provide superior reinforcement in rubber compounds, enhancing properties like tensile strength and abrasion resistance. In contrast, acidic carbon black may offer better dispersion and compatibility in specific polymer systems, leading to improved processing and end-use performance.
Benefits and Drawbacks
The benefits of using acidic carbon black include improved compatibility with specific polymers and additives, leading to enhanced processing and performance characteristics. However, the presence of acidic groups can sometimes lead to undesirable reactions with certain materials, limiting its use in specific applications.
IV. Contrasting Basic and Acidic Carbon Black
Direct Comparison of Properties and Characteristics
When comparing basic and acidic carbon black, the primary distinction lies in their surface chemistry. Basic carbon black has alkaline functional groups, while acidic carbon black features acidic functional groups. This difference significantly impacts their interaction with polymers and additives, influencing material properties and performance.
Impact on Performance and Applications
The basicity or acidity of carbon black affects its reinforcing capabilities differently. Basic carbon black tends to provide superior reinforcement in rubber compounds, enhancing properties like tensile strength and abrasion resistance. In contrast, acidic carbon black may offer better dispersion and compatibility in specific polymer systems, leading to improved processing and end-use performance.
V. Influence on Product Performance
Mechanical Properties of Materials
The choice between basic and acidic carbon black significantly impacts the mechanical properties of materials. Basic carbon black enhances tensile strength, tear resistance, and durability, making it ideal for high-stress applications like tires. Acidic carbon black, while also reinforcing, may excel in applications where improved dispersion and compatibility are critical, such as in specialized rubber formulations and high-performance coatings.
Durability, Strength, and Performance Indicators
Both types of carbon black contribute to product durability and strength, but their specific properties make them suitable for different applications. Basic carbon black’s superior reinforcement capabilities make it indispensable in heavy-duty applications, while acidic carbon black’s compatibility and dispersion advantages cater to niche markets requiring precise material characteristics.
In conclusion, understanding the differences between basic carbon black and acidic carbon black is vital for optimizing material performance and selecting the right reinforcing filler for specific industrial needs. Basic carbon black, with its alkaline nature, excels in enhancing tensile strength and durability, making it ideal for robust applications like tire manufacturing. Acidic carbon black, with its acidic functional groups, offers improved compatibility and dispersion, catering to specialized applications requiring specific interactions with polymers. By recognizing these distinctions, manufacturers can make informed choices, ensuring optimal product performance and meeting diverse industry demands.
Previous page:Carbon Black Uses: A Comprehensive Guide
Next page:Is Carbon Black Synthetic?